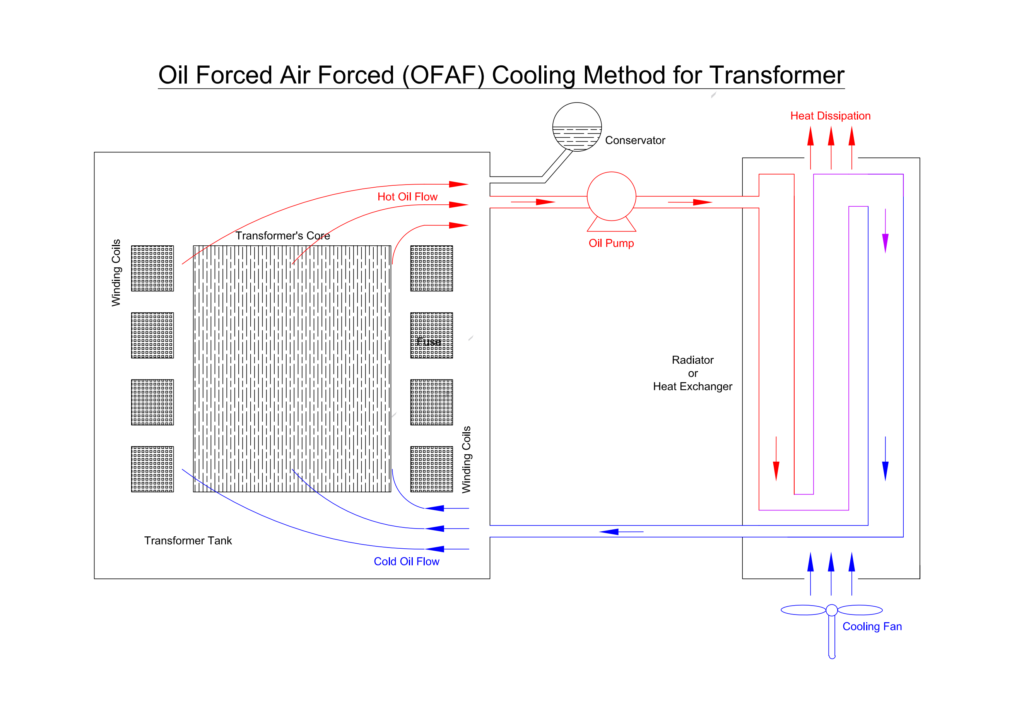
Transformers are critical electrical components used in power systems for transferring energy between circuits, changing voltage levels, and adapting currents for various applications. A deeper understanding of transformers’ cooling methods, operational parameters, and safety measures can help optimize their efficiency and lifespan. Here, we’ll cover key aspects of transformer operations, focusing on electromagnetism, cooling protocols, protection, and insulation requirements.
1. Transformer Principle: Electromagnetic Induction
Transformers operate based on the principle of electromagnetic induction, wherein they convert one AC voltage level to another while maintaining the same frequency. Inside the transformer, a primary winding receives the input voltage, which creates a varying magnetic field. This magnetic flux induces a secondary voltage across the secondary winding, allowing a different voltage and current output while keeping the energy transfer efficient.
The core of the transformer is often made of laminated steel to reduce eddy current losses and improve magnetic coupling between windings, ensuring minimal energy loss. The induced voltage depends on the turns ratio of the windings, enabling effective voltage transformation while minimizing energy dissipation.
2. Cooling Methods and Conditions for Transformer Operation
Cooling systems are essential for maintaining transformer efficiency, especially in large, high-voltage applications. Various cooling methods include natural oil cooling, forced oil cooling, and oil-immersed air cooling. Different types of transformers have specific temperature limits, and understanding these limits can prevent overheating and prolong the equipment’s life.
- Main Transformer Cooler Shutdown Protocol
When the main transformer cooler is completely shut down, it is typically allowed to operate at rated load only within the lower load limit. If the load is low, allowing for an upper oil temperature increase to the specified limit, the transformer can run up to an hour. Monitoring the load and oil temperature during cooler shutdowns helps avoid overheating. - Oil-Immersed Cooling Systems
For oil-immersed self-cooled and oil-immersed air-cooled transformers, the highest allowable oil temperature is 95°C, though it is generally advisable to keep it under 85°C. This limitation prevents the breakdown of insulating materials within the transformer and ensures a stable thermal environment. - Forced Oil Circulation Cooling
In forced oil circulation cooling systems, the upper oil temperature should ideally remain below 75°C and should not exceed 85°C. Forced oil circulation systems use pumps to move the oil through cooling fins or radiators, enhancing heat dissipation and enabling higher load capacities.
These guidelines are crucial for operators to ensure safe, continuous operation of transformers across varying loads and environmental conditions.
3. Buchholz Protection and Secondary Circuit Earthing
Buchholz protection is a safety mechanism for detecting faults in oil-filled transformers, primarily for gas accumulation caused by internal arcing. In cases where a secondary circuit has an earthing fault, Buchholz protection should switch from tripping mode to a signal mode. This setting minimizes unnecessary shutdowns, ensuring that transformer operation is only halted for serious issues, thereby protecting the system without risking disruption from minor faults.
4. Voltage Control and Allowable Limits
For a transformer’s primary winding, the applied voltage should not generally exceed 105% of the rated value on the tap. This control limits the strain on insulation and prevents overheating, which could otherwise compromise the transformer’s integrity. When operating within this margin, the secondary winding can carry the rated current without additional risk, maximizing the transformer’s load capacity while preserving its efficiency and lifespan.
5. SF6 Gas Properties and Usage in Transformers
Sulfur hexafluoride (SF6) is a non-toxic, colorless, odorless, and non-flammable gas with exceptional insulation and arc-quenching properties, making it ideal for high-voltage transformers and other switchgear applications. SF6’s molecular stability allows it to withstand high temperatures and pressures without decomposing, making it an effective dielectric medium. However, handling SF6 requires caution due to its global warming potential, which is significantly higher than CO₂. Proper containment and disposal are essential to prevent environmental impacts while maintaining safe insulation standards【21†source】.
Tips for Transformer Maintenance and Safe Operation
- Regular Inspections
Routine inspections, including temperature checks and oil quality analysis, are essential for identifying early signs of overheating, insulation degradation, and oil contamination. - Monitoring Load Levels
Avoid exceeding rated loads, and maintain load levels within safe operational limits to prevent overheating. This practice also supports the longevity of internal components and prevents costly repairs. - Testing and Calibration
Calibrate protection relays and regularly test Buchholz protection for accurate fault detection. Ensuring that the secondary circuit earthing remains intact helps in avoiding unnecessary tripping and maintaining optimal performance. - Oil Quality Control
Periodically analyze the oil quality for moisture content, acidity, and dielectric strength, as oil quality directly impacts insulation and cooling efficiency.
Conclusion
Transformers are vital components in power systems, supporting energy transformation and distribution at various voltage levels. By following these principles of electromagnetic induction, adhering to temperature and cooling limits, and implementing proper safety protocols, transformers can operate effectively with minimal downtime and lower maintenance costs. Understanding the role of SF6, oil cooling methods, and protection systems can help maintain transformer efficiency and longevity.